Per chi ama lo sci l’espressione «quattro passi» evoca uno scenario mitico, il giro della Sella Ronda, in Trentino, che attraversa quattro passi alpini: il Sella, il Gardena, il Campolongo, il Pordoi. Quaranta chilometri (26 di piste) da percorrere senza togliersi dai piedi gli sci e soprattutto gli scarponi. In attesa che gli impianti riaprano, gli sciatori potranno solo ricordare quando ansimavano felici tra le discese e le seggiovie dei mitici quattro passi, chiedendosi magari quanti passi hanno fatto gli scarponi che hanno appena comprato invano per arrivare nelle loro case.
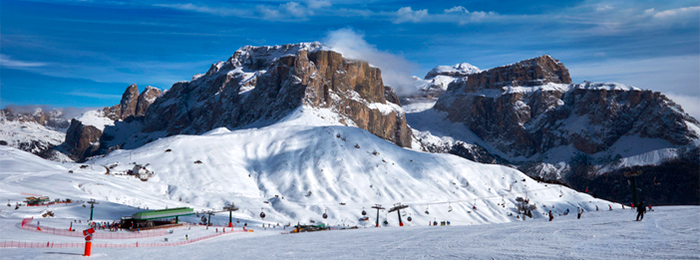
Dal cuoio alla plastica
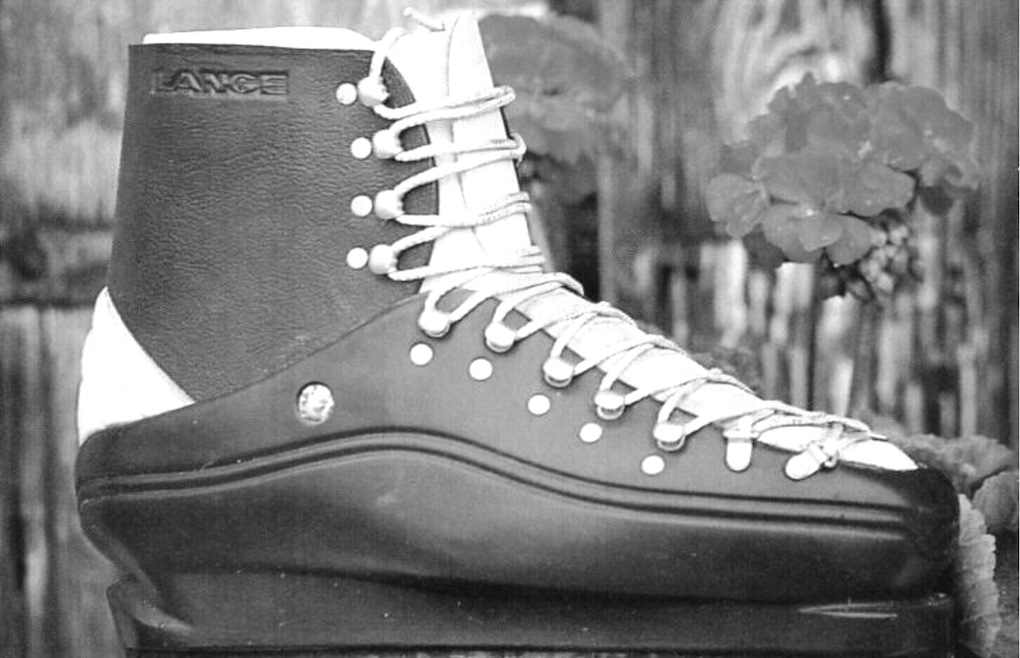
Perché il cammino degli scarponi da sci è completamente cambiato da quando, nel 1965, l’americano Bob Lange realizzò il primo paio di scarponi di plastica, facendo colare del poliuretano in uno stampo.
Prima c’erano quelli in cuoio, derivati dalla pedula da montagna, con qualche adattamento per fissarli agli sci. Da trasportare c’era soltanto il cuoio ai fabbricanti di scarpe sportive. Poi tutto è diventato chimica e tecnologia: il che significa che oggi quella dello scarpone verso lo sciatore è assai più che una passeggiata.
La culla del 65% degli scarponi mondiali
In Italia, per esempio, ogni anno si vendono 200 mila paia di scarponi da sci (223.083 nella stagione 2018-2019), per la maggior parte prodotti nel distretto di Montebelluna, in provincia di Treviso, 16 comuni tra il Piave e il Montello, 120 mila abitanti spalmati su 355 chilometri quadrati, che concentrano nella calzatura sportiva le loro attività: 344 imprese, 2 miliardi di fatturato, 5 mila addetti, uno ogni otto famiglie. Numeri che hanno consentito al distretto veneto di arrivare a realizzare il 65% della produzione mondiale di scarponi da sci, delocalizzando la produzione low quality (scarpe da ginnastica a basso costo e accessori standardizzati) e attirando nell’area anche famosi produttori stranieri di attrezzatura per gli sport alpini.
Resine in movimento
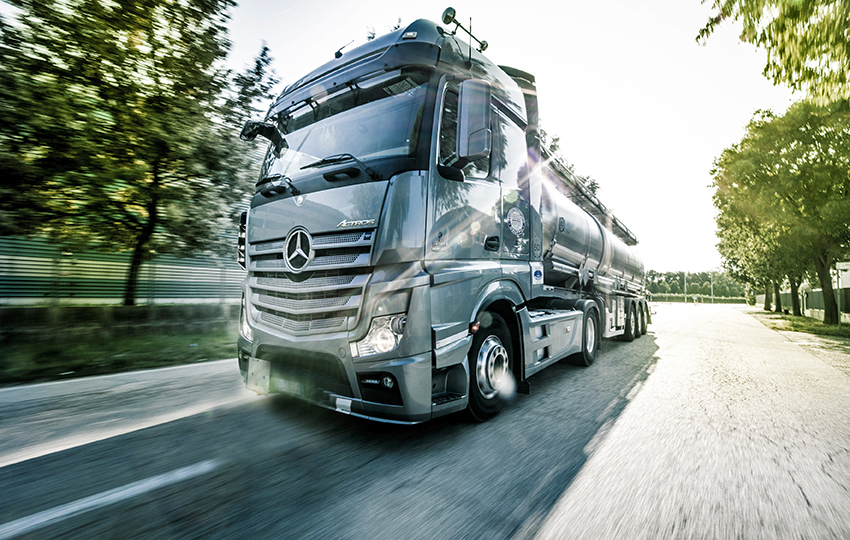
Ma la parte più importante della loro passeggiata, gli scarponi non la percorrono da Montebelluna ai negozi di articoli sportivi di tutto il mondo, quando sono ormai venuti alla luce da una stampante 3D, allestititi con borchie e ganci di chiusura, inscatolati e pallettizzati. No, il cammino più delicato è quello che avviene – come sempre, del resto – durate la gestazione. Dai tempi di quella colata di poliuretano che Bob Lange riversò in uno stampo, oggi il procedimento è diventato più complesso e più raffinato: sia per la scocca esterna (più rigida) che per la scarpetta interna (più morbida) si usano resine provenienti dalla raffinazione del petrolio. Anche gli ultra sofisticati scarponi in fibra ottica hanno bisogno delle resine fra uno strato e l’altro di fibra.
Alla base di tutte c’è lo stirene, un idrocarburo aromatico che si presenta come un liquido oleoso, trasparente e dall’odore dolciastro. Si chiama anche «stirolo» e si fa più presto a capire di che si tratta, quando si polimerizza (cioè diventa una molecola più grande) e viene chiamato «polistirolo». È lui – lo «stirene» o «stirolo» (ma anche «feniletilene» o «vinilbenzene») – alla base delle resine di cui è costituito lo scarpone da sci: la scocca, per esempio, è realizzata con ABS, una plastica molto rigida e resistente, la cui sigla significa «acrilonitrile-butadiene-stirene». Appunto.
Dunque le fabbriche di scarponi ne hanno un bisogno vitale e gliene occorrono grandi quantità: ogni scarpone pesa tra i 2,5 e i 4 chilogrammi e per la maggior parte è in plastica dura, il che vuol dire che di ABS ne occorre una quantità oscillante tra le 1.000 e le 1.500 tonnellate che le industrie chimiche devono fornire al distretto di Montebelluna, ricavandola dallo stirene che arriva nei loro magazzini in autocisterne con il rombo rosso con la fiamma delle merci pericolose. Perché lo stirene – qualunque nome si adoperi – è infiammabile e maleodorante.
GAM, la chimica a 360°
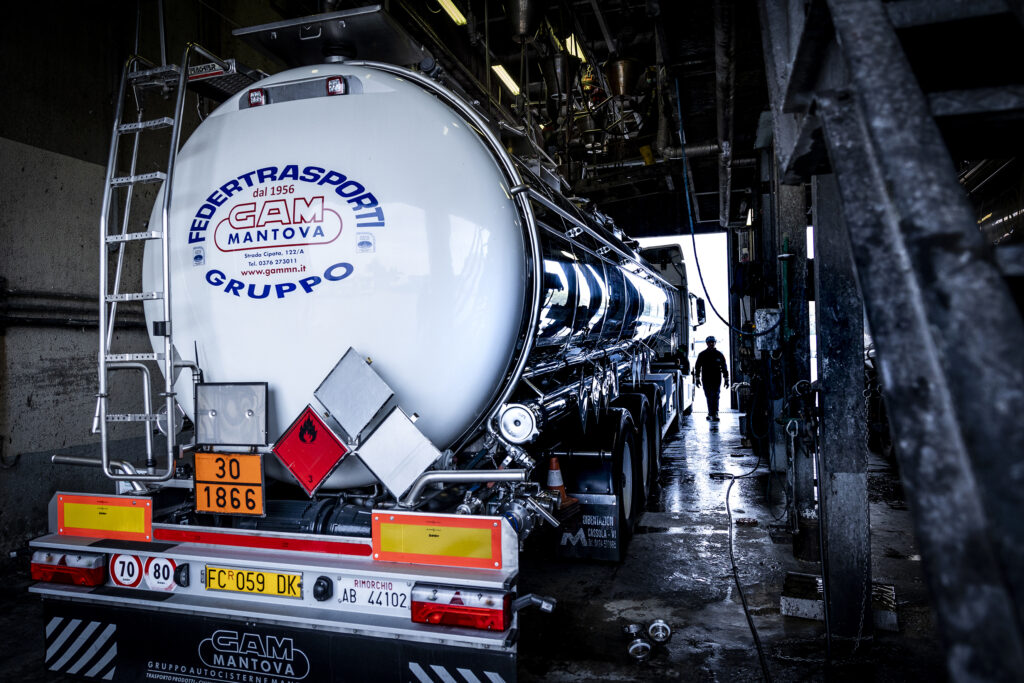
«Lo carichiamo con manichette a circuito chiuso, per impedire contatti umani e dispersioni nell’ambiente, anche se l’unico rischio di inquinamento è quello odoroso», spiega Marco Vincenzi, responsabile Qualità, Sicurezza e Ambiente del Gruppo Autocisternisti di Mantova (GAM), una società cooperativa specializzata nel trasporto di prodotti chimici (impiegati non solo per gli scarponi, ma anche per mobili, vernici, automotive e così via) che impiega 150 veicoli in acciaio inox coibentati, sottoposti continuamente a lavaggio, bonifica e degasificazione, mettendo alla loro guida autisti formati con patentino ADR e adottando protocolli molto rigidi anche in azienda.
Una pianificazione semestrale allergica all’incertezza
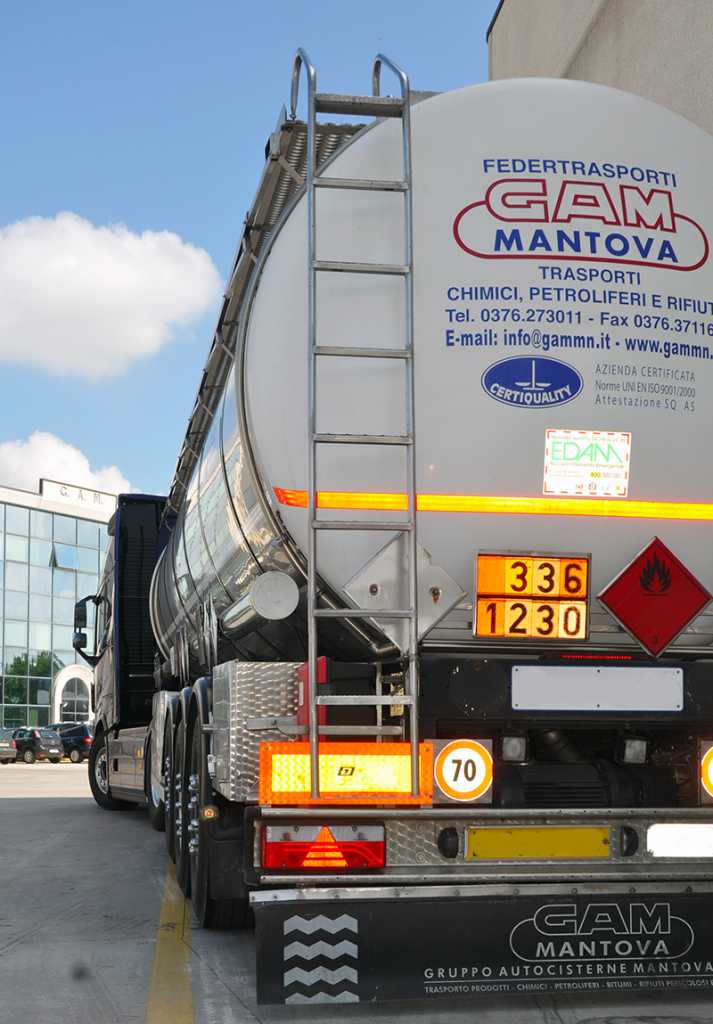
Un’attività intensa e accurata che nella produzione degli scarponi da sci precede di circa sei mesi la nascita del prodotto finale. Lo stirolo e le resine che GAM trasporta ad altre industrie chimiche di trasformazione o ai rivenditori (che poi riforniscono i produttori di scarponi) deve essere modificato nel materiale da usare nella fabbricazione finale. Ci vuole tempo, insomma. E tanti viaggi. Per questo GAM, che al 99% trasporta liquidi non alimentari, non ha risentito in maniera sensibile del primo lockdown, ma subito dopo – tra aprile e maggio – alcune aziende, nell’incertezza sulla futura stagione, non hanno fatto ritirare i prodotti ordinati. In autunno è rinata la speranza, la produzione si è rimessa in moto e anche il mercato degli scarponi si è ripreso.
Ma l’ulteriore rinvio e l’incertezza del futuro hanno di nuovo rallentato tutto. I nuovi modelli non sono usciti nel cassetto dei progettisti. Le autocisterne non hanno caricato lo stirolo. Bisognerà aspettare il prossimo autunno. Per quest’anno bisognerà accontentarsi.
Ti potrebbe interessare anche:
I viaggi della crostata | #cosedifiliera
RACCONTATECI LA VOSTRA STORIA
Siete anche voi protagonisti di una filiera particolare e poco conosciuta?
Dedicate al trasporto di un oggetto un’attenzione e una cura speciale?
Avete voglia di raccontarci viaggi e movimenti delle cose che trasportate verso il quotidiano degli italiani?
Mettiamoci in contatto.
Proponete la vostra storia a: redazione@uominietrasporti.it
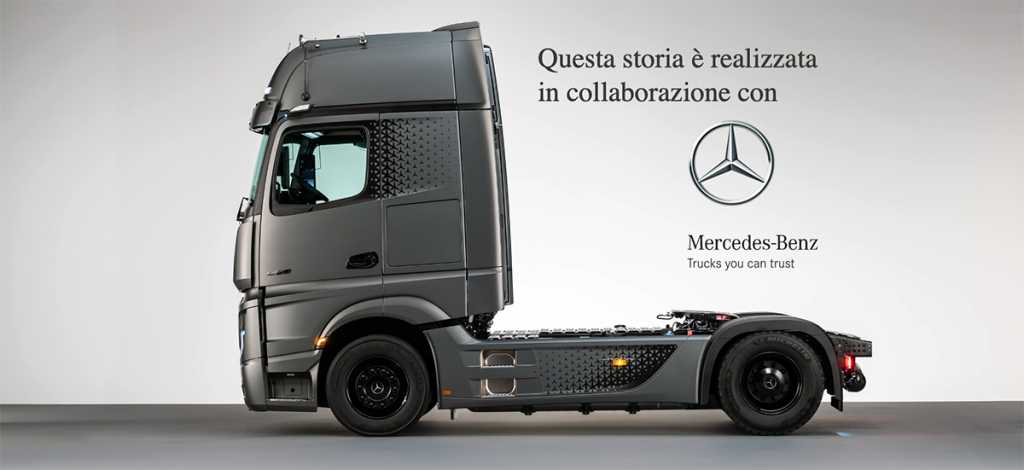
vi dà appuntamento al 21 gennaio 2021