All’interno della piccola cittadina di Garchizy, in piena regione della Borgogna, siamo andati a visitare il luogo dove i motori Iveco ormai consunti e fuori uso vengono rigenerati e tornano a nuova (e a volte migliore) vita.
Qui al centro della Francia si trova infatti uno dei quattro stabilimenti mondiali di Fpt Industrial (gli altri sono a Torino, Springfield e Santo Andrè, in Brasile) che ricevono le carcasse dei propulsori per veicoli leggeri e pesanti della casa torinese. Come vedremo, i motori vengono disassemblati, puliti, sostituiti in alcune parti, rimontati e testati a lungo a caldo (45 minuti, quando solo il 3% dei motori nuovi viene provato e per soli 360 secondi) per vedere che tutto sia a posto. Alla fine, esce un motore come nuovo che verrà reimmesso sul mercato.
La fabbrica Reman ha insomma fatto del processo di rigenerazione dei componenti – propulsori in primis, ma anche altri – una vera e propria arte. Come spiega Davide D’Onghia, responsabile qualità dello stabilimento transalpino, “rigenerare i componenti non significa ripararli, ma farli funzionare come se fossero nuovi. Solo la nostra struttura ufficiale dedicata può garantire un tale livello di qualità, in linea con le più recenti specifiche di primo impianto”.
Tutti i motori, in linea di massima, possono essere sottoposti al procedimento di rigenerazione, purché siano integri nei componenti fondamentali – albero motore, albero a camme, blocco, testa, a prescindere dai chilometri percorsi. Altri elementimaggiormente soggetti a usura, come ad esempio i pistoni, le valvole di aspirazione e scarico, i cuscinetti principali, le guarnizioni dell’albero e altro ancora, sono invece sostituiti con pezzi nuovi.
I vantaggi del rigenerato
Ma quali sono i vantaggi della rigenerazione? Innanzitutto che i ricostruiti Reman costano in media 30% in meno rispetto a un motore nuovo, mantenendo alta qualità e ottime prestazioni. Inoltre i propulsori hanno una garanzia di tre anni e possono avere anche due vite. Poi la rigenerazione consente in media di risparmiare l’80% dell’energia che sarebbe stata utilizzata per produrre un pezzo nuovo, con una riduzione delle emissioni di 28 milioni di tonnellate. Infine i ricambi originali Reman Parts, pronti per essere montati, contribuiscono a ridurre i tempi di fermo macchina.
La qualità del prodotto
I tre pilastri su cui si regge il motore rigenerato Reman sono l’alto livello di know-how dei tecnici, la sistematica integrazione delle specifiche di ingegneria e il continuo aggiornamento tecnologico degli addetti.
I componenti principali del motore vengono sottoposti a rigorosi e ripetuti processi ispettivi, oltre che a fasi di pre-lavaggio e lavaggio dopo lo smontaggio completo della carcassa nella prima area dell’impianto, da cui partono due linee, una per i motori dei veicoli leggeri e una per quelli dei veicoli pesanti.
Le procedure messe in campo, una parte delle quali manuali o semi-automatiche, prevedono anche l’esame accurato delle parti principali, che possono essere sottoposte pure ad analisi metrologiche.
Inoltre tutti i pezzi che arrivano alla linea di assemblaggio sono certificati conformi prima della consegna, anche se il test a caldo finale, effettuato su un banco prova specifico e su ogni singolo propulsore, permette di individuare eventuali anomalie.
Il tempo medio per la produzione di un motore di ricambio è compreso tra le 20 e le 40 ore a seconda dell’applicazione.
Come avviene il processo di rigenerazione: il lavaggio
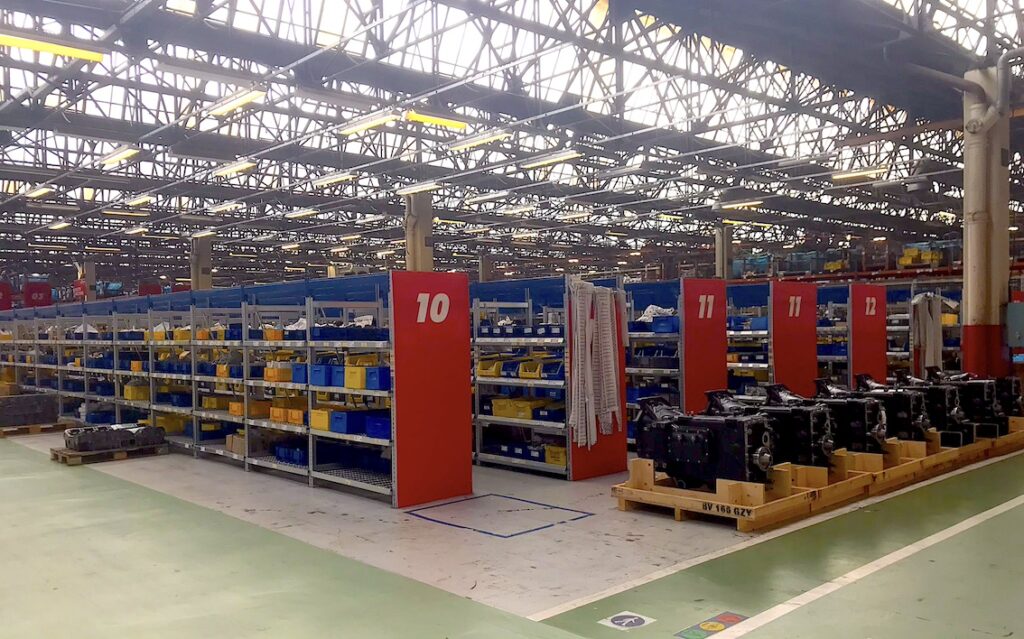
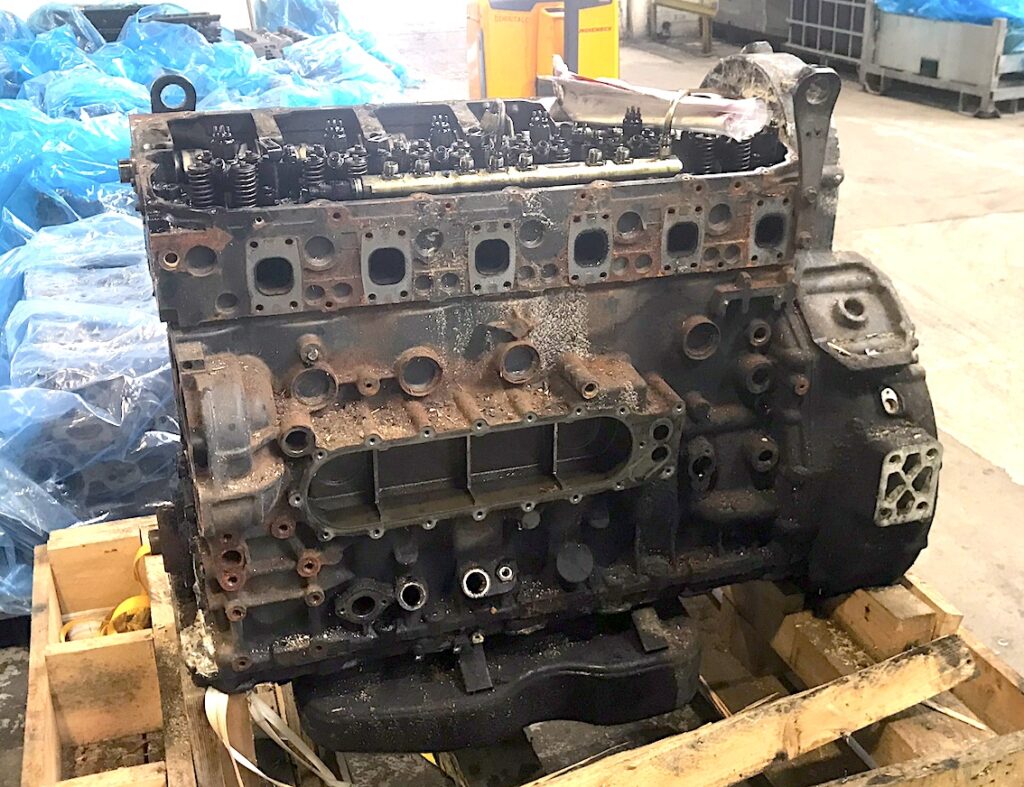
In relazione alla richiesta del cliente, le carcasse che arrivano vengono, come accennato, disassemblate e distribuite sulle due linee, con i componenti usurati che sono cambiati al 100%. La linea di montaggio è costituita da diverse stazioni, parzialmente automatizzate.Si inizia con il lavaggio delle parti, differente a seconda dei materiali che vanno puliti. Si utilizzano diverse tecniche al riguardo: sabbiatura, ultrasuoni e macchina di lavaggio a 6 bagni. In caso di residui, c’è anche un processo di spazzolatura per migliorare l’aspetto finale del prodotto.
Controllo e lavorazioni
Si passa poi ad una fase di controllo di ogni singolo elemento per individuare e valutare piccole crepe o cavità, cospargendo l’albero a gomiti con un liquido di rilevamento fluorescente ai raggi ultravioletti.
C’è poi la lavorazione del blocco, con i cilindri che vengono ricoperti e levigati, seguita a sua volta dalla lavorazione della testa del cilindro, con rivestimento rifatto ex novo, i cuscinetti sostituiti e un test di tenuta sulla sede della valvola (che può essere cambiata in caso di non conformità). Poi vengono rilavorati l’albero a motore, se necessario, e controllate le bielle (diametri, spaziature, piegature, ecc.). Anche le parti non toccate (tubi, supporto filtro, coperchio volano) vengono ispezionate visivamente per capire se sono utilizzabili.
Una particolare procedura riguarda infine le pompe a iniezione, smontate e pulite con macchine specifiche a ultrasuoni, poi riassemblate con nuove guarnizioni. Stessa sorte per il turbocompressore.
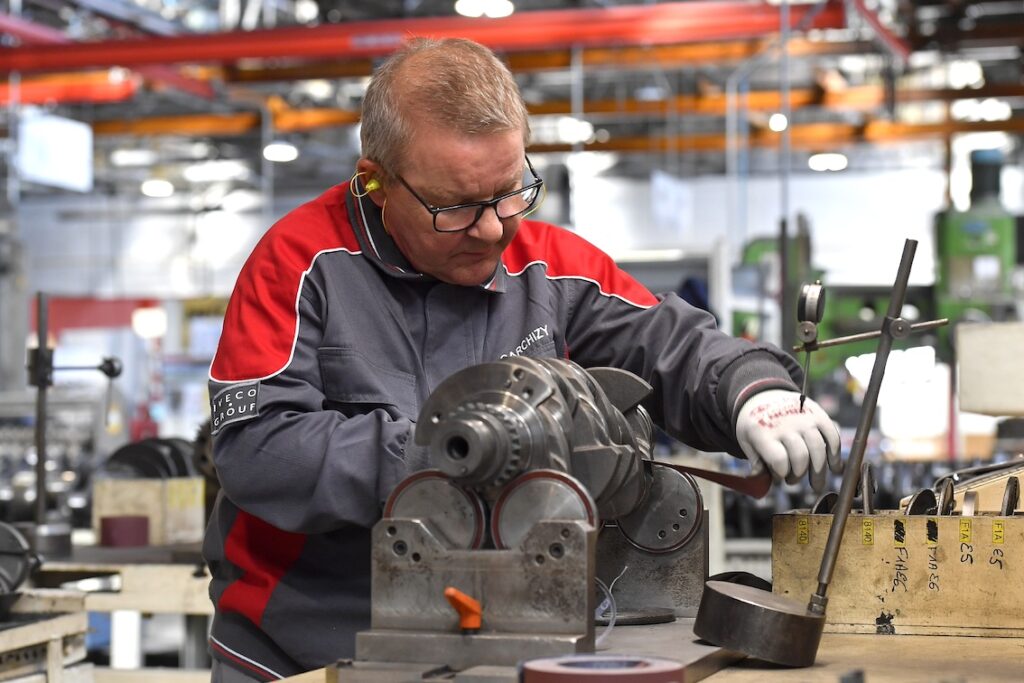
La fase finale
A questo punto avviene l’assemblaggio del motore, con otto stazioni in linea per i leggeri e otto per i pesanti, e il montaggio dei cambi. Il motore ricostruito viene sottoposto a un «leakage test» che individua eventuali perdite prima di un successivo test a caldo, che per circa 45 minuti monitora coppia, potenza, pressione dell’olio, consumo di carburante e così via. Infine i motori dei pesanti vengono verniciati e imballati per il trasporto.
Non solo motori
A Garchizy, Fpt Industrial non rigenera soltanto motori, ma anche altri elementi della catena cinematica, come i componenti elettronici, freni, trasmissioni, turbocompressori, impianti di scarico e sistemi di iniezione.
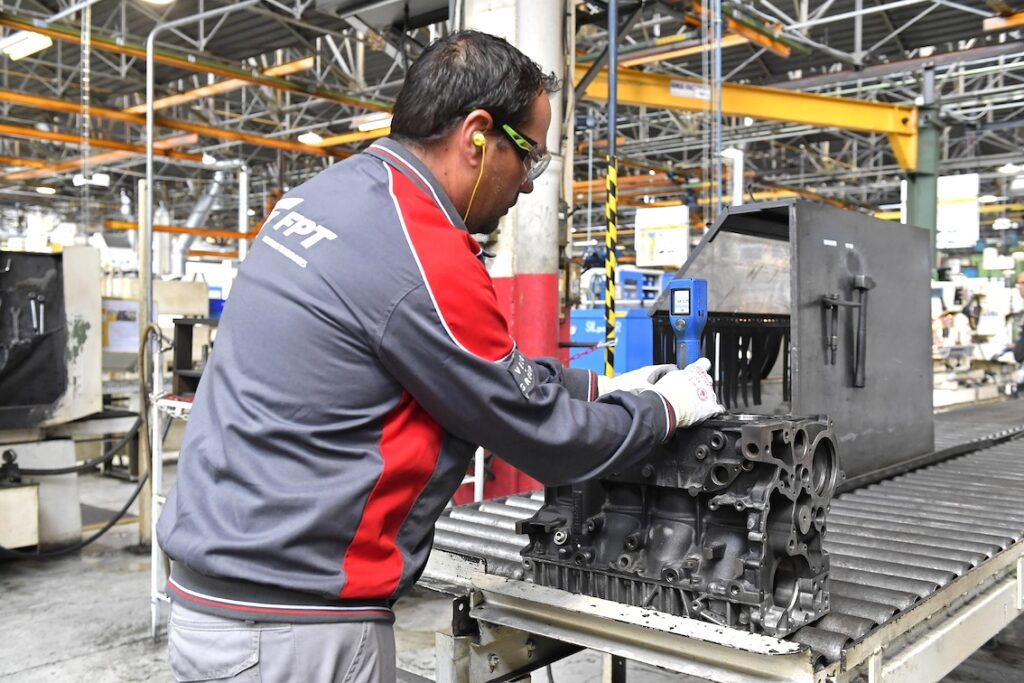